Achieving supersonic speeds presents some engineering challenges. In the supersonic regime, an aircraft exceeds the speed of sound, referred to as Mach 1. The speed of sound is affected by temperature and the medium it's traveling through. When an aircraft reaches Mach 1, shock waves are created, which affect the aerodynamic forces and create a noisy sonic boom on the ground. Because of these effects, commercial aircraft typically operate at speeds around Mach 0.8.
Aside from the effects of exceeding Mach 1, one of the biggest challenges is getting to Mach 1 and beyond. For an aircraft to reach supersonic speeds, afterburners play a key role.
The Basics of a Jet Engine
An afterburner system allows additional fuel to be burned in the engine. To understand how this element helps improve engine performance, it's essential first to know how a classic jet engine works. Jet engines generally consist of four key elements mounted in sequence: a compressor, a combustion chamber, a turbine, and a nozzle. Air passes through the compressor, which is pressurized before entering the combustor. Fuel is then injected into the air and burned in the combustion chamber or burner. The air then passes through the turbine, generating mechanical energy to drive the compressor, before exiting the engine through the nozzle. This entire process generates enough thrust to fly at a given speed by overcoming air resistance or drag.
Afterburner Integration for Enhanced Thrust Capacities
Engines have a maximum thrust that they are capable of reaching. Destinus-3 will use a CJ610 engine. This engine can produce a total thrust of 13 kN; however, more than this thrust is needed to achieve the supersonic regime.Therefore, an afterburner is added to the engine. Located after the turbine and before the exhaust, it allows additional fuel to be injected into the air passing through it, increasing the overall thrust. Destinus engineers have calculated that it could help boost the engine's thrust by about 45 percent. Adding the afterburner also means replacing the old nozzle with a new one with variable geometry. The geometry of the new nozzle can adapt to whether or not the afterburner is activated.
Fuel Injection and Supersonic Speed Attainment
The Destinus 3 engine will operate with an integrated afterburner system. An initial injection of kerosene into the main combustion chamber will be followed by a second injection of liquid hydrogen (LH2) into the afterburner. The liquid hydrogen is supplied from a 75kg LH2 tank. The primary goal is to turn on the afterburner during the cruise mode, allowing the engine to reach supersonic speeds of about Mach 1.3.
Design, Manufacturing, and Testing for Hydrogen-Powered Flight
Destinus engineers have designed the afterburner to be fully adaptable to hydrogen power and it is ready to be manufactured. The diffuser, combustion chamber, and exhaust nozzle are also the components of the tailor-made afterburner.
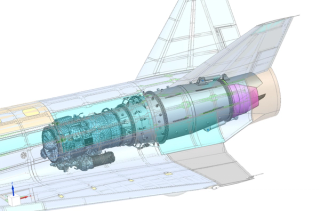
After the manufacturing process is complete, it will undergo extensive testing at Destinus’ newly established hydrogen propulsion test site in Payerne, Switzerland. The system is tested first with gaseous hydrogen (GH2) and then liquid hydrogen (LH2). The goal is to ensure afterburner’s thermal performance and accurately measure thrust generation. The tests are the last essential step to confirm the effectiveness and safety of the afterburner before it can be used in the air.